Step 3 - Model Setup
In Step 1 and 2 we have created a model of the flexure that we wish
to optimize, now in Step 3 we need to prepare this model for the finite
element analysis. Applications (from the tool bar) followed
by Mechanica and Structure invokes the integrated
mode of Pro/MECHANICA. Here we define everything necessary for the design
optimization. Selecting Model lets us define the geometry to
be analyzed.
Constraints
We will start with the constraints, i.e. how the flexure is held in
place. To simulate the flexure's operation, we will constrain the left
end completely, i.e. keep this surface completely from moving. Use Model
-> Constraints -> Create -> Face/Surface and pick the
face at the left end of the flexure. Hit Done Select to confirm
your selection and use the constraint window to set the boundary conditions.
We want to keep this surface from moving, so we constrain it in the
X,- Y- and Z-direction. Solids (3-D elements) do not have a rotational
degree of freedom (unlike 2-D or 1-D elements), so the settings for
RotX, RotY and RotZ will have no effect on
the analysis.
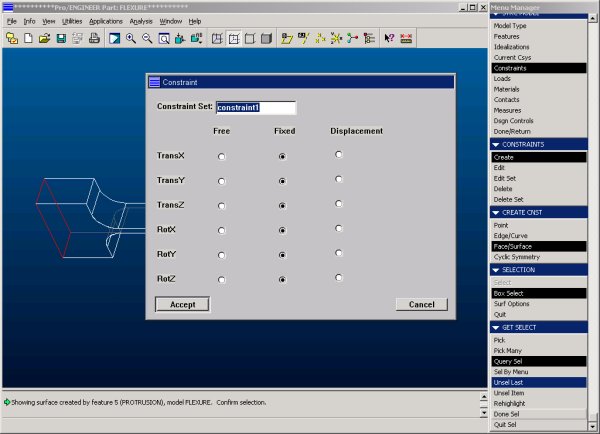
The right end we will constrain in the X- and Z- direction and impose
a displacement of 3 mm in the Y-direction. Note that an analysis can
only be defined with a single constraint set. If more than one feature
needs to be constrained, the same constraint set (here: constraint1)
has to be used.
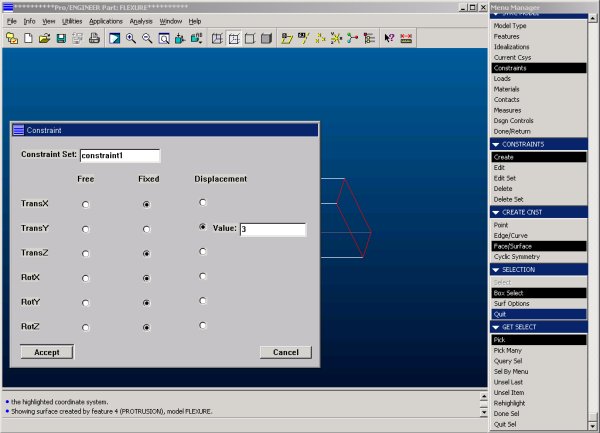
Material Properties
Next we need to assign material properties to our model. In this case
we will make the flexure out of stainless steel. Pro/MECHANICA has a
limited selection of pre-defined materials that we can choose from.
Material sets not found will have to be created by ourselves, using
the same unit system selected in step 1.
Note: For the N-mm-s system, the correct density will have
to be given in tons per cubic millimeter to maintain the consistency
of the units.
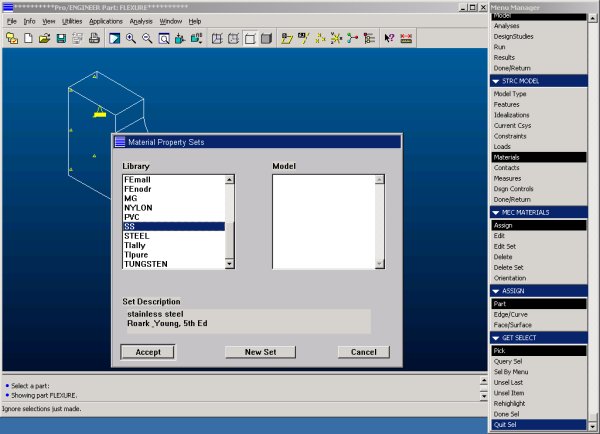
Accepting the material will open up the material property window.
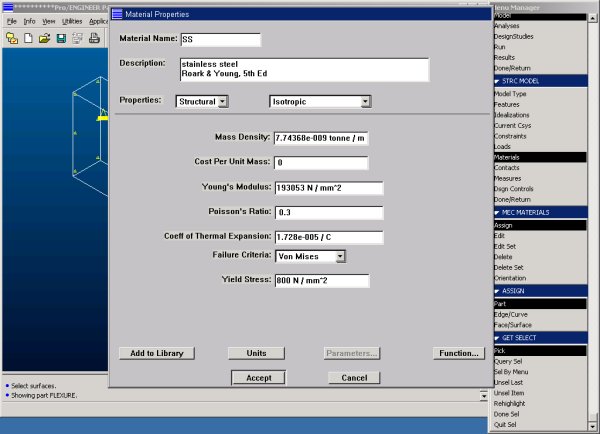
Design Parameters
In order to use the design parameters set up in step 1, we first must
make them available to Pro/MECHANICA. This is done through Model
-> Dsgn Controls -> Design Params -> Create. The type
of parameter needs to be set to Pro/ENGINEER. A window will pop up and
show all available parameters.
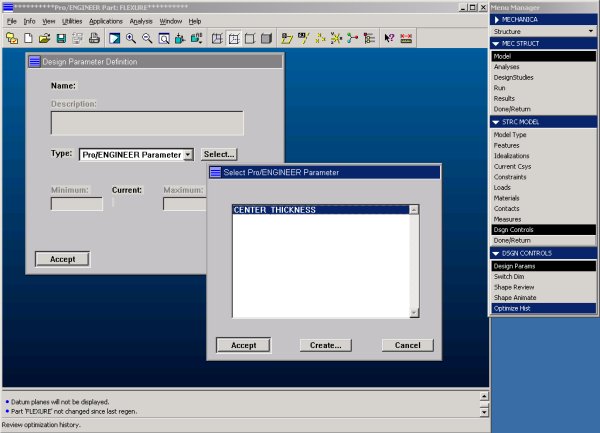
After the selection, the lower and upper limit for this variable will need
to be set.
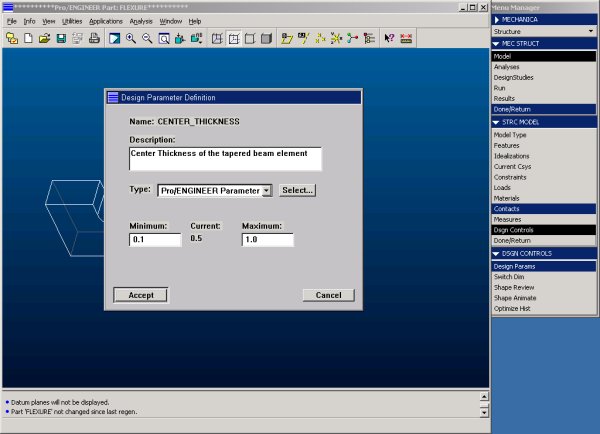
Measures
We can use MECHANICA also to determine the force required to displace
the right side of the flexure by 3 mm. This is done by defining a measure
which tracks the reaction at one of the two constraints.
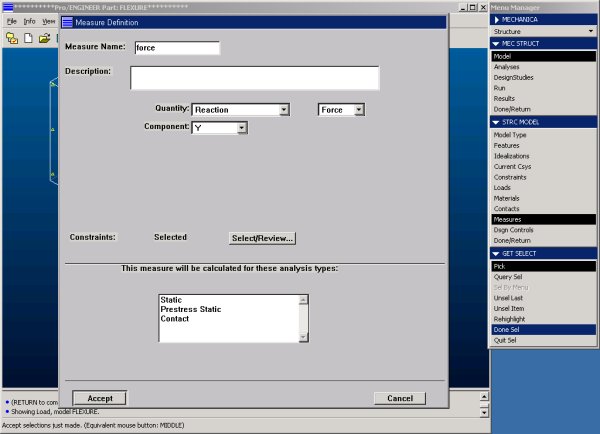