Ph.D. project of Dinesh Rakwal
This project seeks to create innovation resulting
in the potential use of wire-EDM in the shaping of germanium boules
and its subsequent slicing into wafers. This method promises the
potential of decreased subsurface damage at the edge of the wafers,
which is thought to be the leading cause for wafer breakage during
handling and a principal cause of latent defects in the orbiting
solar cell applications. A second benefit of the proposed machining
process is the potential for better flatness of the wafers, which
allows the wafers to be cut thinner compared to conventional methods,
while simultaneously reducing the amount of material to be removed
to achieve the required flatness. A third advantage of wire-EDM
is the fact that the wire used in the process (25-50 μm diameter)
is significantly thinner than the diamond-coated wire currently
in use (150 μm). This allows considerably more wafers to be
cut from s single boule, thereby increasing the production yield
and decreasing manufacturing cost. Using wire-EDM to shape the
boule and slice the wafers has a fourth, potentially very beneficial
aspect: Most excess material removed is in the form of large pieces
which have a better potential for recoverability compared to the
dust that is produced with conventional, abrasive machining processes.
If performed economically, this "green" process will
reduce waste and further reduce manufacturing cost.
Germanium wafers have a similar lattice constant
as gallium arsenide (GaAs), making it a perfect substrate for GaAs-based
multi-junction solar cells which are used on virtually all U.S.
space-based defense, civil and commercial satellites. As such,
multi-junction solar cells are considered to be a defense-critical
technology that requires the establishment of a U.S. domestic capability
to fabricate the precision germanium substrates critical to multi-junction
cell fabrication. However, current production of germanium wafers
suffers from extremely poor yield. This is, in large, due to the
fact that Ge-production processes were designed for use with Si
manufacturing in mind. Germanium, however, is considerably more
brittle than silicon, causing a noticeable portion of the wafers
to break during handling, heating, and other fabrication processes.
It is widely believed that the cylindrical grinding which is required
to shape the boule to its final diameter, introduces damage below
the machined surface. This subsurface damage, which can easily
extend 50-70 microns into the material, triggers microcracking
along the edge of the wafer. These cracks propagate as a result
of stresses that occur during handling, causing the wafer to fracture
catastrophically.
Conventional boule shaping through cylindrical grinding
and wafer slicing with a wire saw:
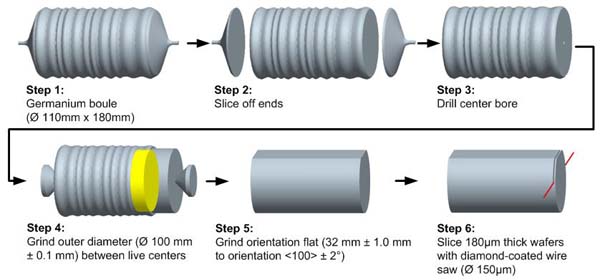
Proposed technique: Wire-EDM for shaping and Slicing:
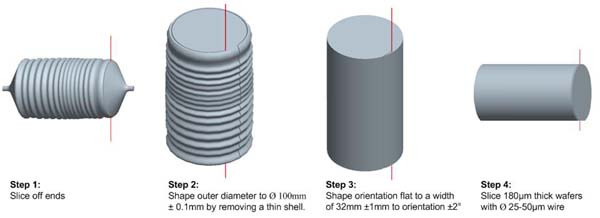

Publications:
D. Rakwal, E. Bamberg (in press). Slicing,
cleaning and kerf analysis of germanium wafers machined by wire
electrical discharge machining. Journal of Materials
Processing Technology. DOI: 10.1016/j.jmatprotec.2008.08.027.
Published online on September 4, 2008.
E. Bamberg, D. Rakwal (2008). Experimental
investigation of wire electrical discharge machining of gallium-doped
germanium. Journal of Materials Processing Technology 197,
pp. 419-427.
D. Rakwal, E. Bamberg (2007). Using
Taguchi methods to optimize the slicing rate and surface roughness
for wire electrical discharge machining of p-type germanium.
In: Proc. 15th International Symposium on Electromachining
(ISEM XV), Pittsburgh, PA, April 23-27, 2007, pp. 127-132.
C. Orino, D. Rakwal, J.D. Jorgensen, E. Bamberg
(2006). Development of a precision, low-cost, small footprint
wire electron discharge machine (WEDM). In: Proc.
2006 ASPE Conf., Monterey, CA, October 15-20, 2006, (26),
pp. 239-242.