The Precision Design Lab focuses on the following research
topics: precision engineering, non-traditional machining of semiconductors,
novel micro- and nanomachining, and biomedical instrumentation.
Piezoelectric
direct drive 3-axis highprecision gimbal
Charles Tschaggeny, M.S. University of Utah,
January 2008
|
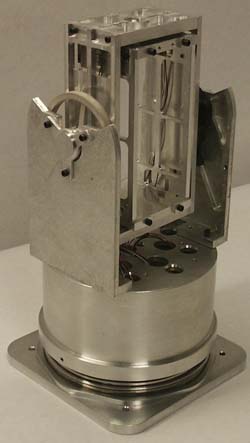 |
|
|
Drum-Type
High-Capacity Magazines For 0.499 Caliber Ammunition For M-4
And M-16 Rifles
M.S. thesis project of Andreas Hellstrand
|
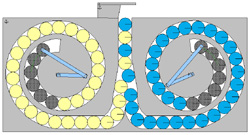 |
|
|
Design
And Optimization Of An Integrated Gear Selector For Mountain
Bikes
Benjamin Mann, M.S. University of Utah, December
2005
|
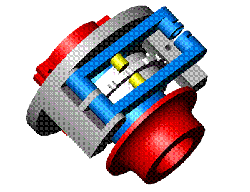 |
|
|
Flexural
Micro-EDM Head For Increased Productivity of Micro-Holes
Sumet Heamawatanachai, M.S. University of Utah,
November 2005
|
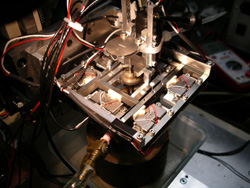 |
|
|
Design
of the High-Capacity, High Caliber LW - 15 Stick Magazine
Clief Castleton, M.S. University of Utah, November
2005
|
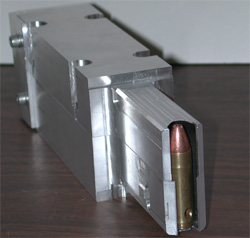 |
|
|
Design
of a Universal Belay Device (Patent Pending)
Nathaniel Young, M.S. University of Utah, November
2005
|
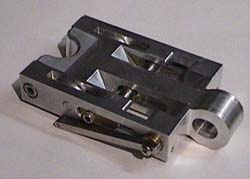 |
|
|
Conceptual
Machine Design Simplification Modeler for Rapid Machine Design
(Patent Pending)
Shreyas Hoskere, M.S. University of Utah, May
2005
|
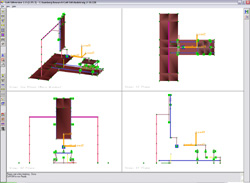 |
|
|
Design Of An Internal Gear
System For Bike Transmission Systems
Michelle Whiteside, M.S. University of Utah,
May 2005
The existing prototype of the integrated gear
selector works well for all but 2 out of 15 gear shifts. Whenever
the chain has to be moved between the front chain rings, the
rider needs to ease up on the pedals in order to allow the
chain to shift (shifts that involve only the rear derailleur
can occur under full load). The solution to this problem is
an internal gear system based on a planetary gear box that
can be shifted under full load as well.
|
|
|
|
Spherical Air Bearing Design
Yuchiang Lin, M.E. University of Utah, May 2005
This project is based on the assumptions of
a linear, non-compressible flow to analytically predict the
flow rate, load capacity, and stiffness of spherical air bearings.
The project investigated the use FLUENT to model such bearings
and compare the results with experimental data.
|
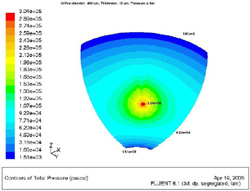 |
|
|
Seamless Integration of Computer
Aided Manufacturing (CAM) into the Mechanical Engineering Curriculum
Zachary Trimble, B.S. University of Utah, May
2005
|
|
|
|
Design
Guidelines for Spherical Aerostatic Bearings
Dinesh Rakwal, M.S. University of Utah, January
2005
|
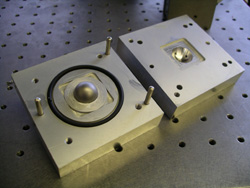 |
|
|
Design
And Testing Of An Adaptive Machining Fixturing System For Surface
Grinders
Xiaofan Xie, M.S. University of Utah, December
2004
|
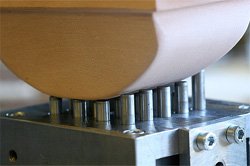 |
|
|
Design
And Testing Of A Micro Machine Tool For Cutting Brittle Materials
Joerg Wiegelmann, Dipl.-Ing. University of Aachen,
September 2004
|
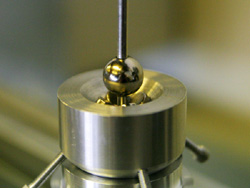 |
|
|
Principles
Of Precision Machine Design Applied To The Design Of A Desktop
Milling Machine
Charan Sarjapur, M.S. University of Utah, August
2004
|
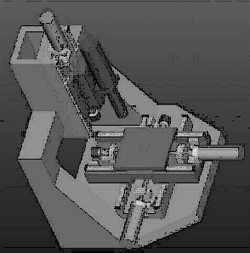 |
|
|
NanoStretcher
Christian Grippo, S.M. MIT, April 2002
A device used to apply and record stresses and
strains in nano-composites while simultanously scanning the
surface with an Atomic Force Microscope (AFM).
|
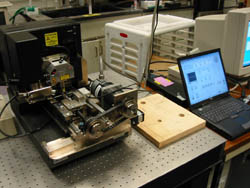 |
|
|
Star
Technolgy Grinder (STG)
Eberhard Bamberg, Ph.D. MIT, May 2000
A 5-axis tool and cutter grinder for the manufacturing
of solid carbide end mills. The novel base design of the machine
is fabricated from round tubes.
|
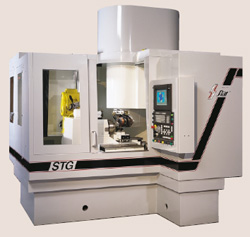 |
|
|
Concrete
CastDamper
Eberhard Bamberg, Alexander Slocum, MIT, 2000
A highly flexible constrained-layer damping
design that is replicated in place through the use of expanding
concrete.
|
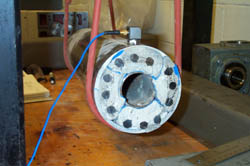 |
|
|
The
TubeMill
Eberhard Bamberg, MIT, 1997
Designed as a lowcost, proprietary milling machine
for the manufacturing of long, tubular workpieces.
|
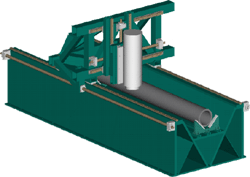 |
|
|
Eberhard Bamberg, MIT 2001
An educational tool used in the teaching of
Mechanics at the Massachusetts Institute of Technology (MIT)
|
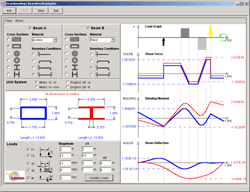 |
|
|
Cutting
Force Predictions
Eberhard Bamberg, University of Stuttgart, 1996
A 32-bit Windows application programmed in Pascal
which predicts cutting forces in milling for various geometries
and materials.
|
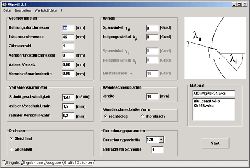 |
|
|
Density
Evaluation
Eberhard Bamberg, University of Stuttgart, 1996
Dichteauswertung (32-bit
Windows) is a tool used to analyze experimental data from cutting
tests. The software reads in arrays of data generated from
force sensors attached to the workpiece fixture and predicts
the wear of the cutting edges.
|
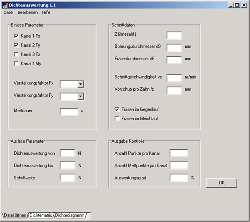 |