Joerg Wiegelmann, Dipl.-Ing., University of Aachen, September 2004
Nowadays, structures below the micrometer range become more and more important. Especially the semiconductor industries demand increasingly smaller structures. The problems are the possible manufacturing methods. However, manufacturing methods capable of producing such small structures tend to be limited to CMOS (Complementary Metal-Oxide Semiconductor)-based systems as a combination of lithography and etching. It is an often used method in the semiconductor industry where still the minimum feature size has not been reached. New developments in beam technologies still offer smaller achievable feature sizes. But these technologies also have some disadvantages and limitations. Aside from the need for toxic chemicals for the etching process and the high costs especially if only a small number of parts are needed, severe limitations for the feature geometry are imposed. The need for a constant feature height, in particular, is a huge limitation of the manufacturing process. It is almost impossible to create features with different heights. Other manufacturing methods are based on scratching where a single-point cutting tool is used to write structures into the sample. As the single point cutting tool, diamond tips with sizes in the nanometer scale are used to create scratches with sizes in the range of a few nanometer. But even these scratching devices are not able to create real three-dimensional features.
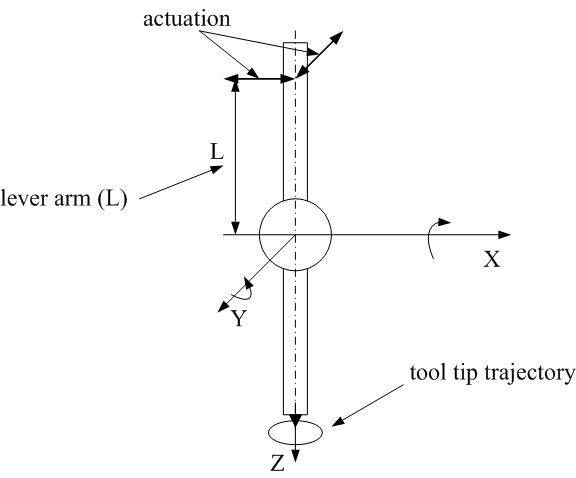
Working principle of MesoMill |
This thesis is about an alternative method of creating real three-dimensional features at a level below one micrometer in a wide range of materials. The new method is also based on a single point cutting tool, but instead of scratching, this method provides a real cutting process. The cutting tip is actuated on a circular trajectory with a variable frequency and a variable trajectory radius. In combination with a relative movement in three dimensions between the tool tip and the workpiece, features with different sizes in width, length and depth are possible. The advantage of this method is the ability of setting the three most important cutting parameters independent of each others: the cutting speed, the feed rate, and the depth of cut. This makes the process in the nanometer range comparable to milling at macro dimensions.
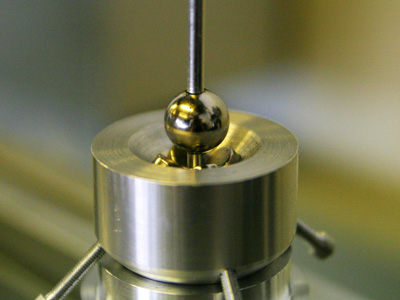
Spherical magnetic bearing prototype 1 |
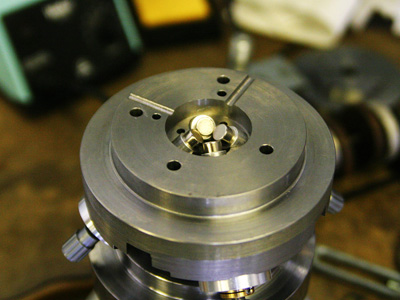
Spherical magnetic bearing prototype 2 |