Design Guidelines for Spherical Aerostatic Bearings
Dinesh Rakwal, M.S. University of Utah, January 2005
Spherical aerostatic bearings are useful in applications involving three rotational degrees of freedom such as satellite motion simulators or a robotic hand joint. The main advantage of using these bearings is low stiction (starting friction), low rotational friction and high stiffness. The analytical theory developed for the design of spherical aerostatic bearings is complex and cumbersome to use for design engineers. The present work uses the Navier-Stokes equations in spherical coordinates while considering the air as a compressible fluid to obtain simple formulas for direct use by the designers. Presented is a detailed analytical and experimental analysis of spherical aerostatic bearings with multiple inlets and outlets. Equations for load capacity, stiffness, flow rate, and pressure distribution for the bearings are derived. Experiments have been conducted by varying several parameters to validate the theoretical formulas developed and to develop design guidelines for these precision machine elements.
The prediction of the pressure at the inlet of the socket is one of the most
crucial and difficult steps in the analytical analysis of any aerostatic bearing.
In this work, the equation for the pressure at the inlet of the socket was
derived and solved by considering air as a compressible fluid for the first
time for spherical aerostatic bearing. The equations developed can be used
for all types of spherical air bearings including fitted type (socket and ball
are of same diameter), clearance type (socket and ball are of different diameter),
single inlet and multiple inlets. Equations for the stiffness of spherical
air bearings using gas as a compressible fluid were derived for the first time.
In general, aerostatic bearings are too complex to analyze theoretically because
of the varying air film thickness which changes as a function of displacement.
Approximating the film thickness as uniform was used to simplify the equations
for various characteristics of the bearings. A correction factor to compensate
for this approximation was derived and a close agreement between practical
and theoretical results was found. Based on the close comparison between theoretical
and experimental results, design guidelines were developed. Existing literature
covers design guidelines of aerostatic bearings such as circular, rectangular,
cylindrical journal and thrust pad bearings, but little information is available
for spherical aerostatic bearings. The guidelines developed for spherical aerostatic
bearings are graphs of the stiffness vs. pressure, load capacity vs. pressure,
and flow rate vs. pressure. The graphs were developed in terms of the bearing
diameter, inlet and outlet angles, orifice diameter, and bearing clearance
for spherical aerostatic bearings. This simplifies the selection process for
spherical air bearings which at present is difficult since no such graphs or
formulas are available that can be used directly. The bearing prototype was
manufactured using a replication process based on epoxy that resulted in a
smooth and accurate spherical bearing surface.
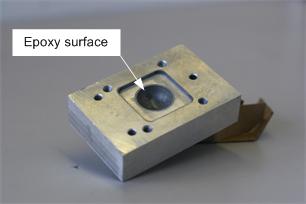
Replicated spherical bearing cavity from low-shrinkage epoxy |
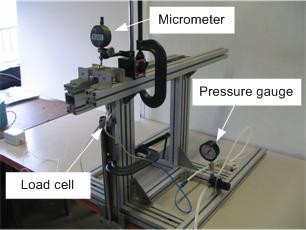
Experimental setup to measure load capacity and stiffness |
Publications
D. Rakwal, E. Bamberg (2005). Design guidelines for spherical aerostatic
bearings. In: Proc. 2005 ASPE Conf., Norfolk, VA, October
10-14, 2005, pp. 170-173.