Star Tool Grinder (STG)
Eberhard Bamberg, Ph.D. Massachusetts Institute
of Technology, May 2000
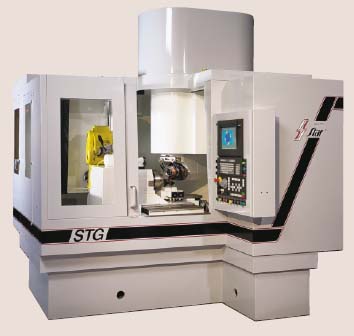
My Ph.D. thesis at MIT, titled Principles
of Rapid Machine Design, presents a set of principles used in
the design and manufacturing of the Star Tool Grinder (STG),
a CNC-controlled
five-axis grinding machine used to manufacture endmills and similar
workpieces. The machine has been designed for a loop stiffness
of 50
N/microns and system modal frequency of above 35 Hz. Using the principles
developed in this research project, the prototype of the STG was
assembled
in less than half the time required for the assembly of the existing
machine, which is going to be replaced by the STG. A great success
indeed!
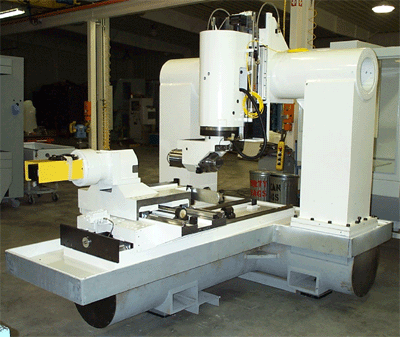
The novel base of the machine consists mainly of two steel round tubes
that are welded together to form a "T". The main beam of the
gantry is made from a round tube as well and provides very high static
stiffness. To ensure high dynamic stiffness, the round tube is equipped
with a constrained-layer damping design called ShearDamper, an internal
damping design.
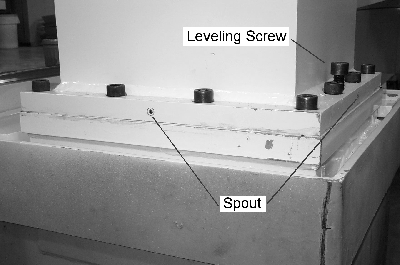
Assembly of the bridge is simplified by replicating the assembly surface
using a high-strength polymer. A thin O-ring between the bridge and
base mounting surface creates a small gap between the two components.
Three leveling screws are used to align the bridge with respect to the
base, and once completed, moglice is injected through four spouts until
the gap between the two mounting surfaces is completely filled. After
the moglice is cured, the leveling screws are removed and the bolts
around the joint tightened.
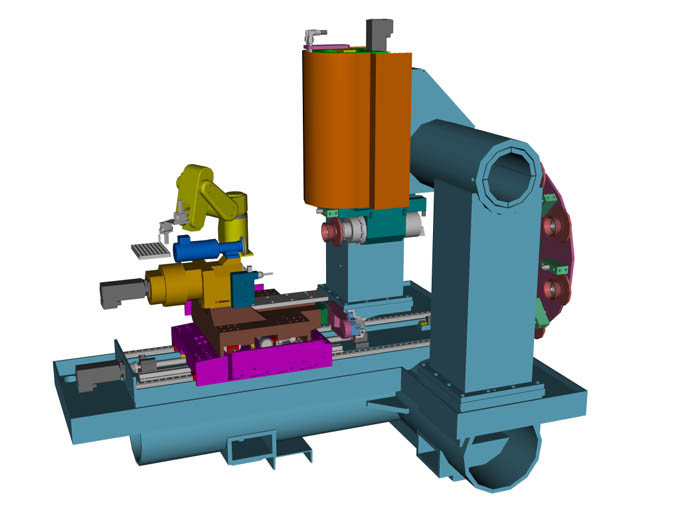
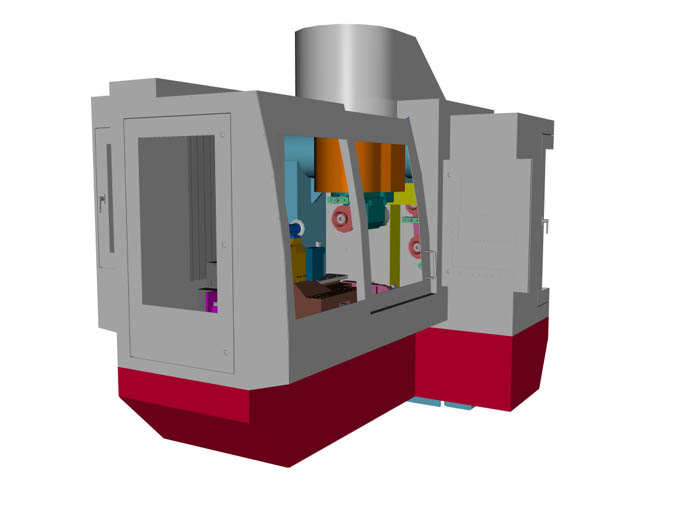
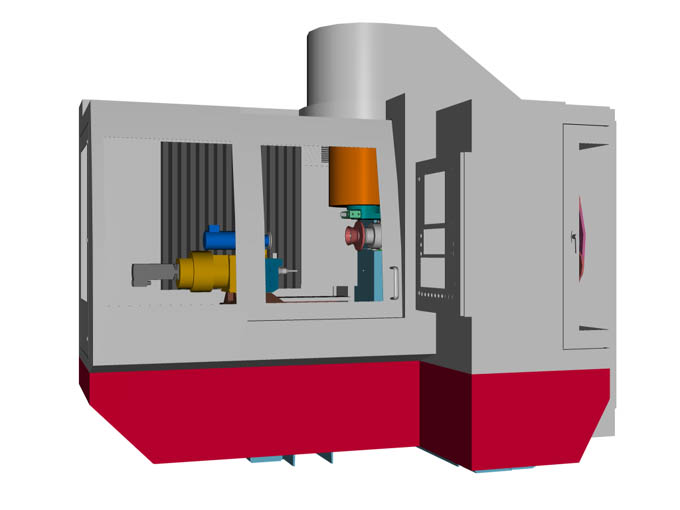
A complete presentation on the
Rapid Machine Design can be found here.