Sumet Heamawatanachai, Ph.D. candidate
This novel micromilling technology is based on single-point
diamond tip milling which can be used to machine microsized features
into a wide range of materials ranging from polymers, through metals
to glass. The unique characteristic of this technology is that
the cutting velocity is not created by rotating the tool tip about
its axis of rotation. Instead, the cutting motion is generated
by actuating the tool tip on a recirculating, microscopic trajectory
at high frequencies. This allows a standard 3-axis setup to generate
the macroscopic motion required for the tool path while at the
microscopic level, the cutting motion and the tool path are being
generated by the tool itself. As a result, truly three-dimensional
part geometries at the micron level with exceptional surface finish
and part accuracy can be created.
The microscopic motion of the tool tip is achieved by a 75 mm long piezo
tube scanner (PZT) made from EC-63 ceramics with an outer diameter of 15.4
mm and a wall thickness of 0.79 mm with four external electrodes. By energizing
the four electrodes with time-varying voltages that range between 0 and
-1000 V, periodic bending of the free end of the tube is achieved. If the
voltages are sinusoidal with a phase lag of 90 degrees between adjacent
electrodes, the resulting periodic bending creates a planar, orbiting motion
with a maximum radius of 35 microns that is perpendicular to the PZT’s
axis. Since the orbiting motion is planar, the machined surface is flat,
making this cutting mode the equivalent of a miniaturized flycutter, whose
tool tip offset from the axis of rotation can be varied during cutting
simply by varying the amplitude of the driving voltages.
Actuating the tool tip with a PZT has another exciting possibility. Overlaying
the sinusoidal driving voltages (primary voltage) with a secondary, time-varying
voltage can be used to periodically change the length of tube in addition
to the bending. This creates a three-dimensional tool path of the tool
tip that can take on a number of very interesting trajectories. For example,
if the secondary voltage has the same frequency as the primary voltage
and is applied to all four electrodes, the periodic change in tube length
creates a planar, orbiting motion that is no longer perpendicular to the
tube’s axis but is tilted instead. This mode allows the machining
of tapered surfaces which in conventional micromilling would require the
use of a tapered endmill or the tilting of either the tool or the workpiece.
Varying the frequency and phase of the secondary voltage creates even more
complicated tool trajectories that can be used to machine free-form surfaces
at the micron level.
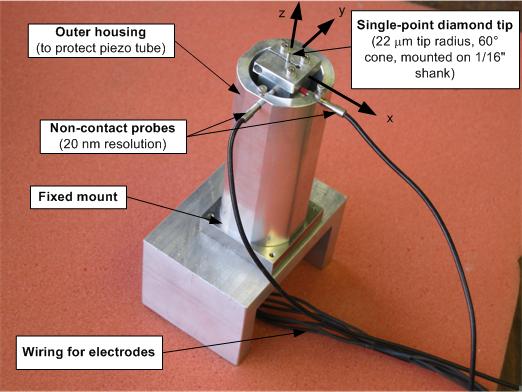 |
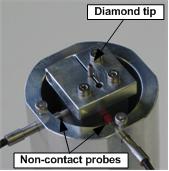 |
Machining examples - stainless steel
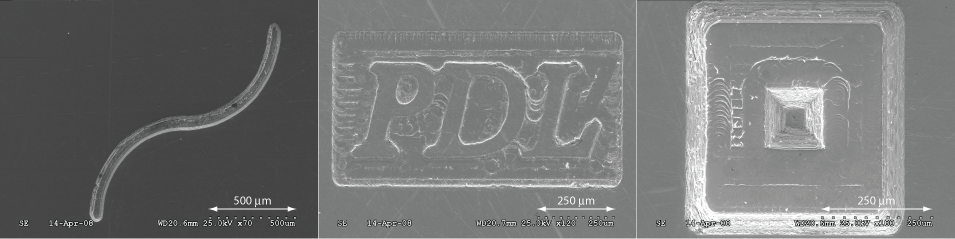
Publications:
S. Heamawatanachai, E. Bamberg (in press). Design
and characterization of a PZT driven micromachining tool based
on single-point tool tip geometry. Precision Engineering.
DOI:10.1016/j.precisioneng.2008.10.006. Published online November
12, 2008.
E. Bamberg, S. Heamawatanachai (2007). A
novel micromilling technology based on single-point tip geometries.
In: Proc. 2007 ASPE Conf., Dallas, TX, October 14-19,
2007, pp. 28-31.